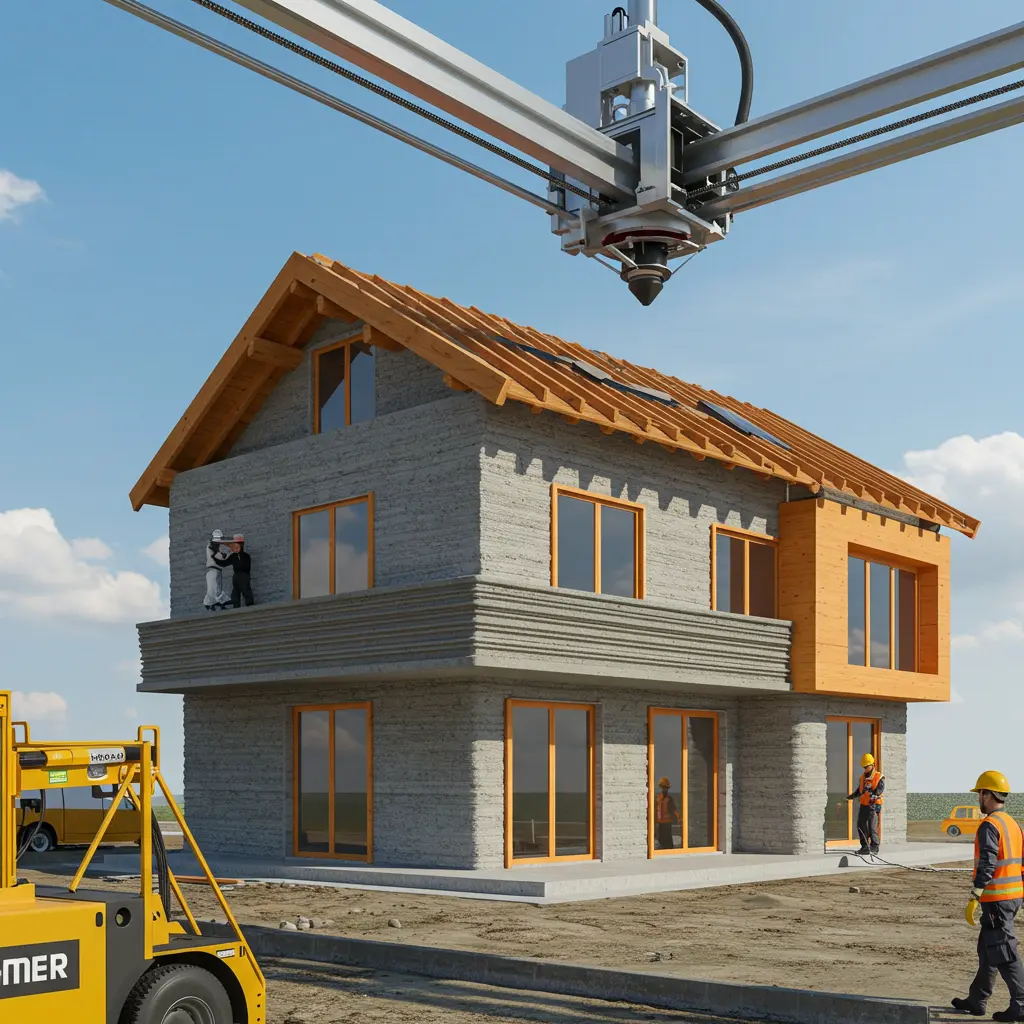
3D-printed houses have been making headlines as a futuristic solution to housing shortages, cost efficiency, and sustainability. However, despite the excitement around this technology, 3D-printed homes have yet to gain widespread popularity and are still overshadowed by traditional wooden and brick construction. But why is that the case? If 3D printing offers such promising benefits, what is holding it back from becoming the mainstream method for building homes?
In this article, we will explore the key reasons why 3D-printed houses are struggling to compete with traditional construction methods.
In this article:
Limited Building Regulations and Code Compliance
One of the biggest roadblocks to the widespread adoption of 3D-printed houses is the lack of standardized building regulations.
- Traditional wooden and brick houses have well-established building codes that have been refined over centuries.
- Most regions have strict guidelines on structural integrity, safety, fire resistance, and material use—many of which do not yet account for 3D printing technology.
- Due to regulatory uncertainty, securing permits for 3D-printed homes can be a slow and difficult process, making traditional methods more practical for contractors and homeowners.
Until construction authorities integrate 3D-printed structures into official building codes, these houses will continue to face resistance from regulators and builders alike.
High Initial Investment in 3D Printing Technology
Although 3D printing is often praised for its cost-effectiveness, the initial setup costs are quite high.
- The price of large-scale 3D printers can range from $200,000 to over $1 million.
- These printers require specialized training to operate, which means additional investment in workforce education.
- Maintenance and material supply chains for 3D printing are still not as established as those for brick-and-wood-based construction.
In contrast, traditional construction companies already have access to affordable materials, skilled labor, and established workflows. Because of this, contractors and developers often find it easier and more financially viable to stick with traditional building methods.
Limited Material Options and Aesthetic Appeal
Most 3D-printed homes today rely on concrete-based mixtures, which limit the range of designs and aesthetics.
- Traditional homes offer a variety of materials such as bricks, wood, stone, and drywall, allowing for greater customization and architectural diversity.
- Many homeowners prefer the classic look and warmth of wood or the durability of brick, making 3D-printed concrete structures less desirable from a design perspective.
- Finishing touches like intricate woodwork, stone facades, and custom roofing are difficult to achieve with 3D printing.
Without the ability to offer the same level of personalization and aesthetic appeal, 3D-printed houses struggle to attract mainstream buyers.
Structural Limitations and Durability Concerns
One of the biggest concerns about 3D-printed houses is their long-term durability compared to traditional homes.
- Traditional wooden and brick houses have been around for centuries, with proven durability in different climates.
- The layer-by-layer printing method used in 3D printing raises concerns about bonding strength between layers, which can affect the structural integrity over time.
- Most 3D-printed houses are single-story structures, while traditional methods easily allow for multi-story homes.
While concrete-based 3D printing is resistant to fire and pests, it remains to be seen whether it can match the century-long lifespan of brick or the flexibility of wooden structures.
Lack of Skilled Workforce and Expertise
The construction industry has relied on traditional skills for generations, and there is a lack of experienced professionals in the field of 3D-printed home construction.
- Carpenters, masons, and bricklayers are readily available in the labor market.
- In contrast, operating and maintaining 3D printing machines requires highly trained specialists, who are currently scarce.
- A shortage of trained 3D-printing operators means fewer companies are willing to invest in this technology.
As a result, the construction industry prefers sticking to well-established methods that have a reliable workforce.
Slow Printing Speed Compared to Expectations
Although 3D printing is often marketed as “fast construction,” the reality is that it is not significantly faster than traditional methods when considering the full construction process.
- While the walls of a 3D-printed home can be completed in a few days, the entire house still requires additional work such as electrical wiring, plumbing, insulation, roofing, and finishing.
- Traditional construction, with an experienced team, can often match or even beat the total time needed for a fully finished home.
Since 3D printing does not eliminate these additional tasks, the speed advantage is not as great as originally expected.
Difficulty in Building Multi-Story Homes
One major limitation of 3D printing is the difficulty in printing multi-story structures.
- The current technology is best suited for small, single-story houses, which limits its use in urban areas where vertical construction is necessary.
- In contrast, traditional wooden and brick structures can be easily scaled to multi-story buildings, making them more suitable for urban housing needs.
Because of this limitation, 3D printing is often seen as an option for low-cost housing or disaster relief shelters rather than a mainstream housing solution.
Supply Chain and Logistics Challenges
The global construction industry has well-established supply chains for bricks, wood, steel, and cement.
- The availability of 3D printing materials is not as widespread, making it difficult to source the right mix of materials in certain regions.
- Transporting a large 3D printer to a construction site is also a logistical challenge, whereas bricks, wood, and cement are easily transported in bulk.
Until 3D printing materials and logistics become more streamlined, traditional construction will remain the more practical option.
Consumer Trust and Perception Issues
Most homebuyers prefer proven and familiar building methods over new and experimental technology.
- People trust brick and wooden homes because they have stood the test of time.
- Many buyers worry about the resale value of a 3D-printed house since it is still an emerging technology.
- There is skepticism about whether 3D-printed homes will maintain their value over decades compared to traditional homes.
Convincing consumers to invest in 3D-printed houses will require years of proven success, which the technology has not yet achieved.
Resistance from Traditional Construction Companies
The existing construction industry is heavily invested in traditional methods and is not eager to embrace disruptive technology.
- Large construction firms have well-established supply chains, labor forces, and profit models based on traditional materials.
- The shift to 3D printing would require a complete overhaul of business models, which many companies see as risky.
- Powerful lobbying groups in the construction and real estate sectors may also resist the rapid adoption of 3D printing technology.
Without major industry backing, 3D printing will continue to struggle against established construction methods.
3D Printing is Still a Niche Solution
While 3D printing has the potential to revolutionize construction, it is not yet ready to replace traditional wooden and brick homes for mainstream housing needs. Key issues such as regulatory barriers, high startup costs, limited material options, and durability concerns have slowed its adoption.
However, 3D-printed houses may still find their place in specific applications such as:
- Low-cost housing projects
- Emergency shelters for disaster relief
- Sustainable eco-homes in remote areas
For now, traditional wooden and brick houses remain the preferred choice for most homeowners and builders due to their proven reliability, flexibility, and market acceptance. Until 3D printing overcomes its current challenges, it will likely remain a complementary technology rather than a dominant force in the housing market.